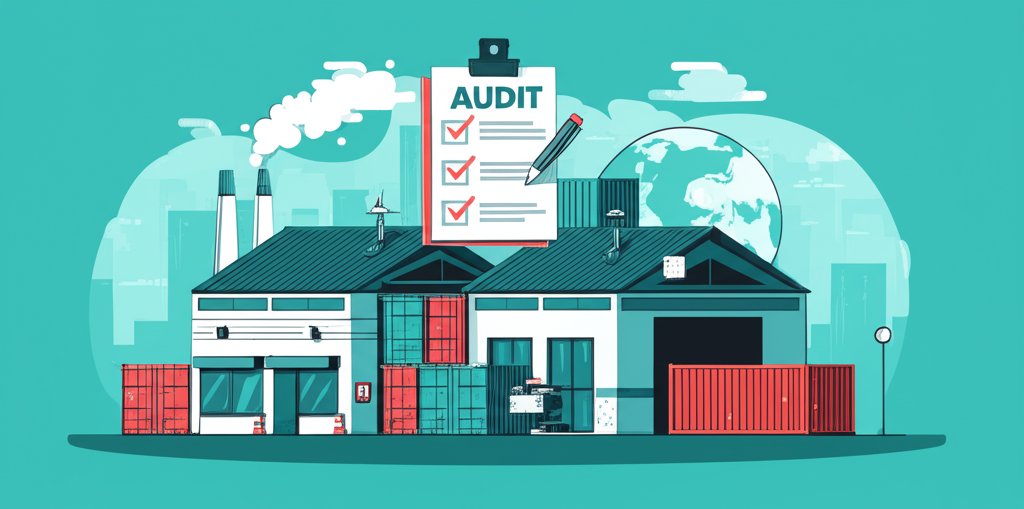
Understanding Factory Audit: The Foundation of Quality and Compliance in Global Sourcing
When you’re sourcing products internationally, how can you be sure your suppliers deliver what they promise—both in terms of quality and ethical practices? This is where the concept of a factory audit becomes essential. Sounds complex? Let’s break down what a factory audit really is and why it’s a cornerstone for businesses navigating today’s interconnected supply chains.
What is a Factory Audit and Why Does It Matter?
Imagine you’re about to partner with a new manufacturer overseas. You want to know: Are their processes reliable? Do they follow safety and labor laws? Will their products meet your quality standards? A factory audit answers these questions by providing a systematic, on-site evaluation of a manufacturing facility. It’s not just a quick walkthrough—it’s a thorough review of operations, safety, compliance, and management systems, all measured against industry standards and your business requirements.
In a global market where supply chains stretch across continents and regulations vary widely, factory audits help businesses:
- Mitigate Risks: Identify and address potential issues before they become costly problems, such as product recalls or supply disruptions.
- Assure Product Quality: Ensure that the manufacturing processes consistently deliver goods that meet your specifications and expectations.
- Support Ethical Sourcing: Verify that suppliers adhere to labor laws, safety regulations, and environmental standards—protecting your brand and supporting responsible practices.
Why Factory Audits Are Critical in Global Supply Chains
You’ll notice that as supply chains become more complex, the risks multiply. Without proper oversight, businesses can face:
- Regulatory penalties for non-compliance
- Damage to brand reputation due to unethical practices
- Operational disruptions from unreliable suppliers
For example, a well-known brand may suffer financial and reputational harm if a supplier is found violating labor laws or producing subpar goods. Regular factory audits help prevent such scenarios by ensuring ongoing compliance and transparency throughout the supply chain. According to industry guides, skipping this step can expose businesses to significant risks, undermining both operational efficiency and stakeholder trust.
Setting the Stage: What’s Next in This Guide?
In the sections that follow, we’ll demystify the entire factory audit process—from defining what a factory audit really entails, to exploring types, checklists, and best practices. Whether you’re new to international sourcing or looking to strengthen your supplier partnerships, understanding what is a factory audit is your first step toward building a resilient, ethical, and high-quality supply chain.
Defining What a Factory Audit Really Entails: Beyond the Basics
When you hear the term factory audit, do you picture a quick visit or a simple checklist? In reality, the factory audit definition goes much deeper—it’s about independent verification. Imagine you’re about to trust a manufacturer with your brand’s reputation. Wouldn’t you want solid proof that they can deliver on quality, safety, and compliance, not just today but in the long run?
What Is the True Meaning of a Factory Audit?
The factory audit meaning centers on a systematic, on-site evaluation of a manufacturer’s ability to meet your business requirements. But it’s more than a box-ticking exercise. At its core, a factory audit is a comprehensive assessment that verifies several key areas:
- Capabilities: Does the factory have the technical know-how, equipment, and skilled workforce to produce your products to specification?
- Compliance: Are they following relevant laws, industry standards, and ethical guidelines for labor, safety, and the environment?
- Management Systems: What systems are in place to control quality, manage risks, and ensure consistent operations?
- Production Capacity: Can the facility reliably meet your volume and delivery timelines, especially as your business grows?
Think of a factory audit as your opportunity to “look under the hood” before making a major commitment—or to check that things are still running smoothly with an existing supplier. This process gives you the confidence to move forward, knowing you’ve minimized risks and set clear expectations.
Factory Audit vs. Product Inspection: What’s the Difference?
You might wonder: Isn’t a product inspection enough? Not quite. While both are important, their focus and timing are different. Here’s a simple comparison:
Factory Audit | Product Inspection |
---|---|
Evaluates the manufacturer’s systems, processes, and long-term capabilities | Checks the quality of products in a specific shipment |
Assesses compliance with standards, regulations, and ethical practices | Focuses on defects, functionality, and appearance of finished goods |
Typically performed before starting or renewing a supplier relationship | Conducted after production, prior to shipping |
So, while a product inspection is like checking the end result, a factory audit is about making sure the whole process is set up for success (Insight Quality).
The Scope and Objectives: Why Businesses Conduct Factory Audits
Why go through this in-depth process? The main objectives for businesses include:
- Risk Mitigation: Identify weaknesses before they cause costly problems, such as late deliveries or product recalls.
- Supplier Qualification: Ensure a new partner is capable and trustworthy before signing contracts or placing orders.
- Continuous Improvement: Monitor ongoing suppliers to catch issues early and drive operational excellence.
- Regulatory and Ethical Assurance: Confirm adherence to labor laws, safety standards, and environmental regulations.
In short, the factory audit definition is all about independent verification—giving you the information you need to make smart, confident decisions in your global sourcing strategy. Next, we’ll walk through the step-by-step process of how these audits are actually conducted, so you can see what’s involved from start to finish.
Walking Through the Standard Factory Audit Process: Step-by-Step Guide
When you hear “factory auditing,” do you imagine a quick checklist or a detailed, multi-step journey? In reality, the factory audit process is a structured series of steps that ensures every critical aspect of a manufacturer’s operations is reviewed. This isn’t just about ticking boxes—it’s about building confidence, reducing risk, and driving continual improvement in your supply chain. So, how does a typical audit unfold from start to finish?
Why a Structured Factory Audit Process Matters
Imagine skipping steps or overlooking crucial details—mistakes like these can lead to costly oversights. That’s why a successful factory audit follows a carefully organized sequence. Each stage builds on the last, ensuring nothing is missed and that results are both reliable and actionable (GoAudits). Let’s walk through each phase so you know what to expect.
The Main Stages of a Factory Audit
- 1. Planning and Preparation
- Define the audit’s scope and objectives—What are you aiming to verify? (Quality systems, social compliance, capacity, etc.)
- Identify which type of audit is needed (system, process, compliance, or technical).
- Set benchmarks and standards to measure against (such as ISO 9001, SA8000, or company-specific requirements).
- Gather necessary resources and background documents (previous audits, supplier records, SOPs).
- Develop or adapt a factory audit checklist tailored to your goals.
- 2. Scheduling the Audit
- Coordinate with the factory to set a date, time, and location.
- Notify all stakeholders—auditors, factory management, relevant staff—so everyone is prepared.
- 3. On-Site Execution
- Opening Meeting: Clarify audit objectives, introduce the team, and outline the day’s agenda.
- Facility Tour: Walk through the production floor, warehouses, and other key areas to observe real-time operations.
- Document Review: Examine policies, procedures, quality records, training logs, and compliance certificates.
- Interviews: Speak directly with management and workers to verify processes and gauge workplace culture.
- Process Observation: Watch how products are made, handled, and checked to ensure procedures match documentation.
- Take notes and collect evidence—photos, samples, and records.
- 4. Reporting Findings
- Compile all observations into a detailed report.
- Highlight areas of compliance and non-compliance, as well as opportunities for improvement.
- Include supporting evidence and clear, actionable recommendations.
- 5. Corrective Action Planning
- Work with the supplier to develop a plan addressing each non-conformance.
- Assign responsibilities and deadlines for corrective actions.
- Establish a monitoring system to track progress and ensure timely resolution.
- 6. Follow-Up and Continuous Improvement
- Schedule follow-up audits to verify that corrective actions have been implemented and are effective.
- Use audit results as a baseline for future assessments, supporting ongoing supplier development and risk management.
Real-World Example: Bringing the Process to Life
Imagine you’re onboarding a new electronics supplier. You start by reviewing their quality certifications and previous audit reports. After scheduling your visit, you spend a day on-site, touring the assembly lines, reviewing training logs, and interviewing workers about safety procedures. Your audit report reveals strengths in process control but highlights gaps in chemical handling. Together, you and the supplier create a corrective action plan, and a follow-up audit a few months later confirms the improvements have been made. This structured approach protects your brand and ensures ongoing quality.
Key Takeaway: Structure Ensures Success
Effective factory auditing isn’t just about finding faults—it’s about setting up a system for continuous improvement, transparency, and trust. By following a clear, step-by-step process, you ensure every audit delivers actionable insights and drives real value for your business. Next, we’ll dive deeper into the different types of audits you might encounter and how each one serves a unique purpose in your supply chain strategy.
Exploring Common Types of Factory Audits: Matching Audit Types to Your Business Needs
When you hear about a factory audit, you might wonder: Are all audits the same, or do they serve different purposes? The truth is, not every audit looks for the same things. Depending on your business goals—whether it’s ensuring product quality, verifying ethical practices, or checking technical capabilities—there’s a specific type of audit designed to deliver the insights you need. Let’s break down the most common types you’ll encounter and what each one focuses on.
1. Quality Management System (QMS) Audit
Ever wondered how a supplier maintains consistent product quality? That’s where a QMS audit comes in. This audit dives deep into the factory’s quality management systems, examining how they control processes, handle documentation, and manage risks. Auditors look for adherence to recognized standards (like ISO 9001), review key production steps, and interview staff to spot gaps or strengths in quality assurance. The main goal? To verify that the supplier can reliably deliver products that meet your specifications and industry standards (Testcoo).
2. Social Compliance Audit
Imagine discovering your supplier is violating labor laws or workplace safety standards. A social compliance audit helps you avoid this scenario. This type of factory compliance audit checks for fair wages, reasonable working hours, safe conditions, and zero tolerance for child or forced labor. Auditors conduct on-site assessments, review HR documents, and interview employees to ensure the factory complies with local laws and international codes of conduct. Many major retailers require these audits to protect their brand and uphold ethical sourcing commitments.
3. Environmental Management Audit
With sustainability on everyone’s radar, how do you know your supplier is minimizing their environmental impact? An environmental management audit assesses whether the factory meets its environmental policies and complies with relevant regulations. Auditors review waste management, emissions control, resource usage, and adherence to standards like ISO 14001. This audit helps you confirm that your supply chain supports environmental responsibility and reduces the risk of regulatory penalties.
4. Security Audit (Including C-TPAT)
Security audits—sometimes called C-TPAT (Customs Trade Partnership Against Terrorism) audits—are designed to evaluate the safety and security of your supply chain. These audits assess facility access controls, cargo handling procedures, and physical security measures to prevent theft, tampering, or terrorism-related risks. Companies involved in international trade often need these audits to meet customs requirements and ensure seamless cross-border operations.
5. Technical or Capability Audit
Ever questioned if a potential supplier can actually produce your product at the right scale and quality? A technical or capability audit answers this by evaluating the factory’s production technology, equipment, workforce skills, and R&D capabilities. Auditors check production capacity, review main processes, and assess whether the factory can meet your volume, lead time, and technical requirements. This audit is especially useful when qualifying a new supplier or introducing a new product line.
6. Supplier Assessment Audit
Before you start working with a new supplier, you’ll want to confirm their legitimacy and capabilities. A supplier assessment audit gathers detailed information on the supplier’s business structure, legal compliance, production facilities, and track record. This type of audit is a critical tool to avoid fraudulent or underqualified partners and to ensure your supplier can meet your expectations for cost, quality, and delivery (Testcoo).
7. VR Factory Audit
Can’t visit the factory in person? VR factory audits use virtual reality technology to provide a 360-degree, real-time view of the facility. This innovative approach allows you to experience key processes, review compliance, and spot potential issues remotely—with professional commentary from auditors guiding you through every detail. VR audits are especially valuable for buyers who need a comprehensive overview but face travel restrictions or time constraints.
How Do You Choose the Right Audit Type?
Still unsure which audit fits your needs? Here’s a quick comparison to help clarify:
Audit Type | Main Focus | Primary Objective |
---|---|---|
Quality Management System | Process control, documentation, risk management | Assure product quality and consistency |
Social Compliance | Labor practices, workplace safety, human rights | Ensure ethical and legal compliance |
Environmental Management | Emissions, waste, resource management | Support sustainability and regulatory compliance |
Security (C-TPAT) | Facility and cargo security | Protect supply chain integrity |
Technical/Capability | Production technology, capacity, skills | Verify ability to meet technical and volume needs |
Supplier Assessment | Business legitimacy, basic compliance | Screen new or existing suppliers |
VR Factory Audit | Virtual facility walkthrough | Remote, detailed factory evaluation |
Bringing It All Together
Each type of audit—whether it’s a factory compliance audit, a factory safety audit, or a technical assessment—serves a unique purpose in protecting your business and building a resilient supply chain. By matching the audit type to your specific objectives, you ensure you’re gathering the right information to make informed, confident decisions. Next, we’ll look at how checklists and templates can further streamline your audit process, ensuring nothing important slips through the cracks.
Leveraging Essential Factory Audit Checklists and Templates for Consistent Results
When you think about conducting a factory audit, do you imagine flipping through endless paperwork or feeling overwhelmed by what to check next? That’s where a well-designed factory audit checklist or factory audit template becomes your best tool. These resources not only keep the process organized but also help ensure no critical detail is overlooked. So, how do these checklists work, and what should they include?
Why Are Checklists and Templates So Important?
Imagine walking into a new supplier’s facility. Without a structured guide, it’s easy to miss key areas—maybe you forget to ask about incoming material inspections or overlook how complaints are handled. A comprehensive checklist brings consistency to every audit, whether you’re visiting a factory for the first time or performing a routine review. It also provides a clear record of findings, making it easier to spot trends, identify risks, and track improvements over time (SafetyCulture).
What Does a Typical Factory Audit Checklist Cover?
While every audit should be tailored to your business needs, most effective checklists share a core structure. Here are the key sections you’ll usually find:
- Quality Management
– Are there robust quality control systems in place?
– How are procedures documented and monitored?
– Are continuous improvement practices evident? - Production Control
– How are workflows managed from raw materials to finished goods?
– Are production processes efficient and well-documented?
– Is there evidence of timely and accurate order fulfillment? - Incoming Material Inspection
– Does the factory check all incoming materials for conformity?
– Are there clear procedures for rejecting or quarantining non-conforming items? - In-Process Quality Control
– Are inspections and tests performed at critical stages during production?
– How are defects detected and managed before final assembly? - Final Inspection and Packaging
– Are finished products thoroughly checked before shipment?
– Is packaging appropriate to prevent damage during transit?
– Are shipping marks and date codes used as required? - Non-Conforming Material Handling
– Are there systems to separate and manage defective or incorrect materials? - Human Resources and Working Conditions
– Are labor practices compliant with local laws and international standards?
– How are health, safety, and training managed? - Facilities and Maintenance
– Is the factory clean, well-maintained, and organized?
– Are equipment and infrastructure regularly serviced? - Communication and Documentation
– Are records, manuals, and reports well maintained?
– Is there effective internal and external communication? - Complaint Handling and Continuous Improvement
– Are customer complaints tracked and resolved promptly?
– Does the factory use feedback to drive improvements?
Some templates even include a scoring system or calculator to help you objectively compare different suppliers and prioritize areas for follow-up (Insight Quality).
Standard vs Custom Checklists: Which Should You Use?
Wondering whether to use a standard template or create your own? Standard checklists, often based on industry best practices or international standards, are a great starting point—especially if you’re new to auditing or need consistency across multiple sites. However, every business is unique. Customizing your factory audit checklist allows you to focus on areas that matter most to your products, brand values, or regulatory requirements. For example, you might add sections on environmental impact or social compliance if those are priorities for your company.
Making the Most of Your Audit Tools
Whether you download a ready-made factory audit template or design your own, remember: the checklist is not just a formality. It’s a living tool that guides your observations, documents your findings, and supports meaningful supplier conversations. At the end of the audit, a sign-off section ensures accountability and helps formalize the process (SafetyCulture).
With a solid checklist in hand, you’ll feel more confident and organized—ready to capture every detail that matters. Up next, we’ll dive into the global standards and requirements that shape how factory audits are conducted, helping you understand what benchmarks to measure against and why they matter for your supply chain success.
Understanding Key Factory Audit Standards and Requirements: What Sets the Benchmark?
When you’re preparing for a factory audit, you might wonder: What are auditors actually measuring your supplier against? Are there universal rules, or does every company make up its own? The answer lies in a set of internationally recognized factory audit standards and well-defined factory audit requirements that guide the process and ensure consistency—no matter where your factory is located.
Why Do Standards Matter in Factory Auditing?
Imagine trying to compare two factories—one in China, one in Europe—without a common yardstick. Standards provide that yardstick. They set clear expectations for quality, safety, social responsibility, and environmental management. By using them, auditors can objectively assess if a facility meets global benchmarks, not just local minimums.
Key International Factory Audit Standards
- ISO 9001 (Quality Management Systems): The gold standard for quality management. ISO 9001 requires factories to have documented processes for ensuring product consistency, continuous improvement, risk management, and customer focus. Auditors check for process controls, staff training, and records of corrective actions.
- SA8000 (Social Accountability): Focuses on fair labor practices and workplace conditions. This voluntary standard covers child labor, forced labor, health and safety, freedom of association, discrimination, working hours, and remuneration. Auditors often interview workers, review HR records, and observe workplace conditions to verify compliance.
- BSCI (Business Social Compliance Initiative): Widely used by global brands to ensure ethical supply chains. BSCI audits cover working hours, fair compensation, occupational health and safety, and environmental protection. The amfori BSCI Code of Conduct is a key reference for these audits.
- ISO 14001 (Environmental Management): Sets requirements for environmental policies, waste management, emissions control, and sustainable practices. Auditors review documentation, waste disposal methods, and energy usage to ensure compliance.
- SMETA (Sedex Members Ethical Trade Audit): Combines elements of labor, health and safety, environment, and business ethics into a comprehensive framework. SMETA is especially popular for retailers with complex, global supply chains.
- C-TPAT (Customs-Trade Partnership Against Terrorism): Relevant for factories exporting to the United States. This standard focuses on supply chain security, including facility access controls and cargo handling procedures.
Core Requirement Categories Audited in Every Factory
Regardless of which standard is used, most audits review similar core areas. Here’s what you can expect:
- Quality Systems: Are there documented procedures for every critical process? How are non-conformities tracked and resolved? Is there ongoing staff training and process improvement?
- Working Conditions: Do employees work in a safe, healthy environment? Are labor laws and ethical guidelines followed, including fair pay, reasonable working hours, and no child or forced labor?
- Environmental Management: How does the factory handle waste, emissions, and resource consumption? Are there policies to minimize environmental impact?
- Facility Security: Are there controls to prevent theft, tampering, or unauthorized access?
- Documentation and Records: Are all required records—training, inspections, incidents—kept up to date and accessible?
How Auditors Evaluate Adherence to Standards
Wondering how auditors actually check compliance? Here’s the typical approach:
- Document Review: Auditors examine manuals, policies, training logs, and compliance certificates to verify that systems exist and are up to date.
- Facility Walkthrough: A physical tour of the site to observe practices in real time—like safety gear usage, machine maintenance, and waste disposal.
- Interviews: Conversations with management and workers to confirm that documented policies are practiced day-to-day.
- Sampling and Testing: Random checks of products or processes to ensure consistency and quality.
For example, during a social compliance audit, an auditor might ask workers about their working hours and compare answers to payroll records. For an environmental audit, they might inspect how hazardous waste is stored and disposed of, matching observations against written procedures.
Bringing Standards and Requirements Together
In summary, factory audit standards and factory audit requirements create a level playing field for evaluating suppliers worldwide. By understanding these benchmarks and how auditors verify compliance, you’re better equipped to select reliable partners and build a resilient, responsible supply chain. Up next, we’ll explore how to interpret the results of a factory audit report—so you can turn findings into practical actions for improvement.
Interpreting Your Factory Audit Report: Turning Insights into Action
Ever received a factory audit report and wondered, “What do all these findings really mean for my business?” You’re not alone. These reports might look technical or overwhelming at first, but with a clear approach, they become powerful tools for decision-making and supplier improvement. Let’s break down how to read, understand, and act on your audit results—step by step.
What Does a Typical Factory Audit Report Include?
Imagine your audit report as a roadmap—it shows where your supplier is strong, where risks exist, and what needs fixing. While formats can vary, most factory audit report formats share a common structure. Here’s what you’ll typically find:
- Executive Summary
– A concise overview of the audit’s purpose, main findings, and overall outcome. This section quickly tells you if the supplier meets your key criteria or if there are serious concerns. - Audit Scope
– Details on what was reviewed—such as quality systems, social compliance, environmental management, or technical capacity. The scope helps you understand which areas the findings relate to. - Detailed Findings
– The heart of the report. Here, auditors list specific observations, both positive and negative. Each finding is usually linked to a standard or requirement (for example, ISO 9001 or local labor laws). Supporting evidence, such as photos or document references, adds credibility. - Non-Conformities and Severity Ratings
– Issues are often classified by severity (major, minor, or critical). Major non-conformities, like missing safety protocols or falsified records, require urgent attention. Minor issues may need improvement but don’t pose immediate risks. - Corrective Actions and Recommendations
– For each non-conformance, the report should outline what needs to be addressed, suggested actions, and deadlines for resolution. This is your action plan for supplier improvement. - Overall Assessment or Score
– Many reports include a summary rating or score, making it easier to compare suppliers or track progress over time. - Supporting Documentation
– Photos, checklists, interview notes, and other evidence that back up the findings.
How to Read and Use Your Factory Audit Report
Sounds like a lot? Don’t worry—here’s how to make the most of your report:
- Start with the Executive Summary: Quickly gauge whether the supplier meets your requirements or if there are red flags that need immediate attention.
- Review the Scope: Ensure the audit covered all areas important to your business—such as quality, ethics, or environmental practices.
- Assess the Severity of Findings: Pay close attention to major and critical non-conformities. These are the issues most likely to disrupt your supply chain or expose you to risk.
- Use the Corrective Action Plan: Treat this as a collaborative roadmap. Work with your supplier to address each point, set deadlines, and monitor progress.
- Leverage the Overall Score or Assessment: Use this to benchmark suppliers, prioritize follow-ups, or track improvements over time.
Why Severity Ratings Matter
Not all findings are created equal. Imagine discovering a minor housekeeping issue versus a major safety violation. Severity ratings help you focus your attention and resources where they matter most. For example:
- Critical/Major Non-Conformities: Immediate action required—these can halt production, cause compliance failures, or damage your brand.
- Minor Non-Conformities: Improvement needed, but not urgent. Address these to support continuous improvement.
Turning Insights into Supplier Improvement
Remember, a factory audit report isn’t just a scorecard—it’s a springboard for improvement. Use the findings to:
- Negotiate corrective actions and timelines with your supplier.
- Monitor follow-up audits to confirm issues are resolved.
- Inform your sourcing decisions—whether to continue, develop, or reconsider a supplier relationship.
- Build a history of supplier performance, supporting long-term risk management.
By understanding the factory audit report format and the meaning behind each section, you’ll be equipped to turn complex findings into clear, actionable strategies. Next, we’ll discuss how to select the right audit service provider—ensuring your reports are thorough, timely, and tailored to your unique sourcing needs.
Choosing Factory Audit Services: What Matters Most for Global and China Sourcing?
When you’re on the hunt for reliable factory audit services, the options can feel overwhelming. How do you separate a truly qualified provider from the rest? Imagine you’re preparing to source from China or another major manufacturing hub—your decision could mean the difference between smooth, compliant shipments and costly supply chain headaches. Let’s break down the essential factors to consider so you can select a partner that fits your business, protects your interests, and delivers actionable results.
What Should You Look for in a Factory Audit Service Provider?
Not all audit companies are created equal. The right partner brings more than just a checklist—they offer experience, industry insight, and the ability to adapt to your unique requirements. Here’s what to prioritize as you compare providers:
- Auditor Experience and Credentials
– Are the auditors certified (for example, ISO 9001) and do they have a proven track record in your industry?
– Look for teams with deep knowledge of both quality control and local compliance standards, especially when sourcing from China (Tetra Inspection). - Industry Specialization
– Does the provider understand the nuances of your product category—be it electronics, apparel, machinery, or consumer goods?
– Specialized auditors can better identify risks and compliance gaps that generalists might miss. - Geographic Coverage and Local Expertise
– For factory audit services in China, does the company have auditors stationed in key manufacturing regions?
– Local teams are more familiar with regional regulations, cultural practices, and common pitfalls—helping you avoid surprises and delays. - Reporting Quality and Transparency
– How clear, detailed, and actionable are their audit reports?
– Look for providers who offer photo-rich, evidence-based documentation, with findings linked to recognized standards and clear corrective action plans. - Turnaround Time and Responsiveness
– Can the provider deliver reports within your required timelines—ideally within 24-48 hours of the audit?
– Responsive communication and fast issue resolution are critical when you’re managing tight production schedules. - Pricing Transparency
– Are rates clearly stated and all-inclusive, or are there hidden fees for travel, expedited service, or additional documentation? – Transparent pricing helps you budget accurately and avoid unpleasant surprises. - Alignment with Your Process and Needs
– Does the provider offer customizable checklists or tailor their audit scope to your business priorities? – The best partners will work with you to define goals, reporting formats, and follow-up actions that fit your supply chain strategy.
Comparing International vs. Local Providers: Which Is Right for You?
As you evaluate factory audit services in China, you’ll notice both international and local companies on the market:
International Providers | Local Chinese Providers |
---|---|
|
|
For many importers and sourcing managers, a hybrid approach—using a provider with both international standards and local presence—offers the best of both worlds.
How to Avoid Common Pitfalls When Choosing a Provider
Imagine discovering too late that your chosen auditor lacks relevant certifications or delivers vague, delayed reports. To prevent this, always:
- Request sample audit reports to assess quality and detail
- Verify certifications and industry memberships
- Ask for client references or testimonials
- Clarify turnaround times and escalation procedures for urgent issues
- Ensure there’s a clear process for addressing non-conformities and follow-up actions
Why Proven Expertise and Transparent Methodologies Matter
Ultimately, the best factory audit services are those that align with your business goals, provide independent and thorough assessments, and communicate findings in a way that supports confident decision-making. Providers with a strong reputation, transparent processes, and deep regional expertise—especially in China—can help you mitigate risk, improve supplier performance, and protect your brand without unnecessary stress or delays.
Ready to take the next step? In the following section, we’ll dive into the unique challenges and best practices for factory audit in China, so you can navigate local regulations and cultural nuances with confidence.
Navigating Specific Considerations for a Successful Factory Audit in China
When you think about a china factory audit, do you picture a process similar to what you’d find in the US or Europe? In reality, conducting a factory audit in China comes with its own set of unique challenges—ranging from regional differences and language barriers to deeply rooted cultural practices and regulatory complexities. Let’s break down what makes auditing in China different, and how you can set yourself up for success.
Why Is a China Factory Audit So Different?
Imagine you’re thousands of miles away, working across a 12-hour time difference, and your supplier’s first language—and business culture—are entirely different from your own. Auditing in China means navigating not just geography, but also the complexities of a government-driven economy, local business customs, and evolving legal frameworks. Here’s what you’ll encounter:
- Language and Communication Barriers: Most factory staff and management communicate primarily in Mandarin or regional dialects. Misunderstandings can easily arise unless your audit team is fluent and culturally aware (CCBJ).
- Cultural Nuances: Chinese business culture emphasizes relationships (guanxi), hierarchy, and face-saving. Direct confrontation or criticism is often avoided, which can make it tricky to get honest answers or highlight non-conformities.
- Regional Differences: China’s vast size means factories in coastal regions like Guangdong may operate differently than those inland, with variations in labor practices, regulatory enforcement, and even business hours.
- Regulatory Environment: The Chinese government controls many aspects of the economy, and local enforcement of laws can be inconsistent or arbitrary. Auditors often encounter challenges accessing reliable documentation, as local banks and officials may prioritize relationships over transparency.
- Document Reliability: Traditional verification methods—like bank confirmations or official records—may not always be trustworthy. It’s not uncommon for documents to be manufactured or for records to be incomplete.
Common Non-Compliance Areas in China Factory Audits
Ever wonder what issues show up most often during a factory audit in China? Here are some frequent red flags:
- Labor Law Violations: Excessive overtime, underage workers, and incomplete payroll records are recurring issues, especially in less developed regions.
- Health and Safety Gaps: Inadequate protective equipment, poor emergency preparedness, and lack of safety training can put workers—and your supply chain—at risk.
- Environmental Compliance: Waste disposal and emissions controls may not meet international standards, particularly in smaller or older factories.
- Quality System Shortcomings: Weak documentation, inconsistent process controls, and lack of continuous improvement practices can undermine product reliability.
The Critical Role of Local Expertise and Specialized Audit Services
Sounds daunting? Here’s where local knowledge becomes your secret weapon. Partnering with a sourcing expert or audit provider with on-the-ground experience in China makes all the difference. Why?
- Language Fluency: Local auditors can communicate clearly, reducing misunderstandings and ensuring you get accurate, actionable insights.
- Cultural Understanding: Experienced professionals know how to navigate sensitive topics, build trust, and interpret subtle cues that outsiders might miss.
- Regional Know-How: Auditors familiar with specific provinces or cities can anticipate regulatory quirks, labor market trends, and logistical challenges unique to each area.
- Innovative Verification: When standard documentation falls short, local experts use creative methods—like third-party analysts or discreet site observations—to validate supplier claims (CCBJ).
Why Specialized China Factory Audit Services Are Essential
Trying to manage a factory audit in China from afar? You’ll quickly find that remote oversight or desktop research just doesn’t cut it. Here’s why specialized audit services are a must:
- Tailored Approach: Providers with deep China experience can customize checklists and audit scopes to address your unique compliance, quality, or ethical concerns.
- Faster, More Reliable Reporting: Local teams can deliver photo-rich, evidence-based reports quickly—often within 24 hours—so you can make sourcing decisions with confidence.
- Risk Mitigation: By identifying hidden issues and verifying supplier claims, specialized auditors help you avoid costly mistakes, protect your brand, and ensure ongoing compliance.
“Conducting a factory audit in China is an essential step towards ensuring product quality, supplier compliance, and ultimately protecting your brand’s reputation.” (Epic Sourcing)
In summary, a successful china factory audit requires more than just technical expertise—it demands local insight, cultural sensitivity, and a flexible, resourceful approach. By working with specialized audit partners who know the landscape, you’ll be equipped to navigate China’s unique challenges and build a robust, reliable supply chain. As we wrap up, let’s recap the strategic value of factory audits and why ongoing diligence is your best defense in global sourcing.
Factory Audits: Your Ongoing Advantage for Quality, Compliance, and Supply Chain Resilience
When you look back at everything involved in a factory audit—from checklists and international standards to on-site assessments and specialized China expertise—it might feel like a lot to manage. But imagine skipping this step: Would you risk product recalls, compliance penalties, or a damaged reputation? The answer is clear. Factory audits aren’t just a one-time hurdle; they’re an essential, ongoing part of supplier management that unlocks lasting value for your business.
Why Factory Audits Are a Strategic Must-Have
Let’s recap the big picture. Factory audits deliver more than just snapshots of compliance or quality—they’re a proactive tool for:
- Assuring Product Quality: Regular audits uncover process flaws and help set clear expectations, so you consistently receive goods that meet your standards.
- Mitigating Risk: By identifying issues early, audits prevent costly disruptions, recalls, and reputational damage.
- Supporting Ethical and Legal Compliance: Audits ensure your partners follow labor laws, safety regulations, and environmental guidelines—protecting your brand and customers.
- Driving Continuous Improvement: Each audit report becomes a roadmap for supplier development, highlighting corrective actions and tracking progress over time.
- Building Supply Chain Resilience: By regularly checking supplier capabilities, you reduce vulnerability to global shocks and ensure reliable delivery—no matter where your factories are located.
Making Audits an Ongoing Part of Supplier Management
Think of a factory audit checklist excel or a detailed factory audit report sample as more than paperwork—they’re living tools that help you benchmark performance, set improvement goals, and keep everyone accountable. By making audits a regular fixture in your sourcing strategy, you’re not just “checking the box”—you’re building a culture of transparency, trust, and operational excellence.
The Value of Experienced Audit Partners—Especially in China
If you’re sourcing from China or other complex markets, working with a seasoned audit provider isn’t just helpful—it’s essential. Local expertise helps you navigate language barriers, regional regulations, and cultural nuances, ensuring your audit goes beyond surface-level checks. A trusted partner can tailor checklists, deliver photo-rich reports quickly, and spot risks you might otherwise miss—giving you the confidence to move forward with new suppliers or strengthen existing relationships.
“Regular factory audits are the cornerstone of a resilient, transparent, and high-performing supply chain.”
Ready to Take the Next Step?
As you plan your next sourcing move—whether onboarding a new partner, expanding to a new region, or reviewing your current supply base—remember: investing in regular audits pays dividends in quality, compliance, and peace of mind. Don’t wait for problems to arise. Instead, leverage proven audit checklists, request a factory audit report sample from your provider, and build a partnership with experts who understand your industry and your sourcing region.
Explore reputable audit service options that offer the transparency, speed, and regional expertise your business needs. By making factory audits a cornerstone of your supplier management program, you’ll not only protect your brand but also unlock new opportunities for growth, efficiency, and long-term success.
Factory Audit: Frequently Asked Questions
1. What is the main purpose of a factory audit?
A factory audit is designed to independently verify a manufacturer’s ability to meet your quality, compliance, and capacity requirements. It provides a thorough on-site evaluation of management systems, production capabilities, and adherence to legal and ethical standards. This process helps businesses reduce risks, ensure consistent product quality, and confirm that suppliers operate responsibly.
2. How is a factory audit different from a product inspection?
A factory audit evaluates the entire manufacturing process, management systems, and compliance with standards before or during a supplier relationship, focusing on long-term capabilities and risk mitigation. In contrast, a product inspection checks the quality and condition of specific goods in a particular shipment, typically after production is complete.
3. What are the most common types of factory audits?
Common types include Quality Management System audits (reviewing process controls and documentation), Social Compliance audits (checking labor and ethical practices), Environmental Management audits (assessing waste and resource management), Security audits (evaluating facility and supply chain security), and Technical or Capability audits (confirming production capacity and technical skills).
4. Why are factory audits especially important for sourcing in China?
Factory audits in China address unique challenges such as language barriers, regional regulatory differences, and cultural nuances. Local expertise is crucial for accurate communication, understanding documentation practices, and identifying common non-compliance issues like labor law violations or environmental gaps. Specialized audit services help importers verify supplier legitimacy and protect their brand.
5. How do I choose a reliable factory audit service provider?
Look for providers with ISO-certified auditors, industry specialization, and strong local presence—especially in your sourcing region. Transparent pricing, clear reporting, and fast turnaround times are key. For China, choose a partner with established networks across major manufacturing hubs, like Eagle Eyes Quality Inspection, which delivers photo-rich, actionable reports within 24 hours and offers all-inclusive rates.