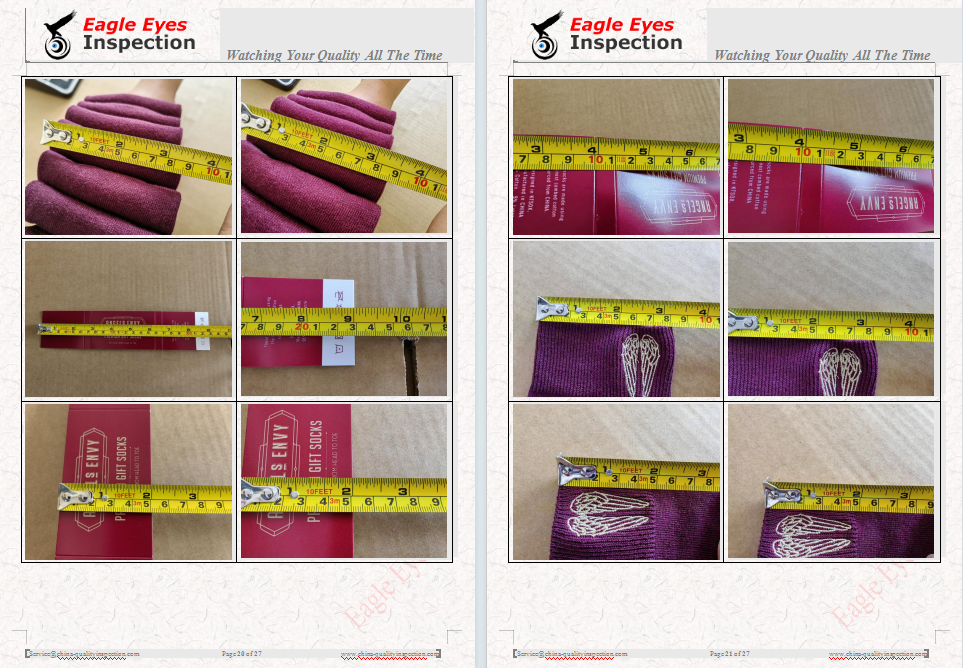
Key Inspection Processes for Socks (QC Checklist)
Here’s a standardized workflow for sock inspection:
1. Pre-Production Inspection (PPI)
Material Verification: Check fabric composition (e.g., cotton, polyester, spandex) against specifications.
Lab Testing: Confirm colorfastness, shrinkage, pilling resistance, and durability.
Sample Approval: Validate stitching, elasticity, and design alignment with tech packs.
2. During Production Inspection (DPI)
In-Line QC: Monitor stitching consistency, seam strength, and pattern alignment.
Size/Weight Checks: Ensure uniform sizing and weight per product standards.
3. Final Random Inspection (FRI) – AQL-Based
(Follow ISO 2859-1 AQL Levels, typically 2.5 for minor defects, 1.0 for major defects)
A. Visual Inspection
Fabric Defects: No holes, stains, or uneven dyeing.
Stitching/Seams: Flatlock seams (no raw edges), reinforced heels/toes.
Print/Embroidery: Logo placement, color accuracy, and symmetry.
B. Functional Checks
Elasticity Test: Cuff retains stretch after repeated use.
Size Measurement: Length, width match spec sheet (tolerance ±5%).
Color Consistency: No shade variation within pairs.
C. Packaging & Labeling
Pair Matching: Socks are correctly paired and folded.
Labels: Care instructions, size tags, barcodes comply with regulations (e.g., EU/US standards).
Polybag Safety: Breathable packaging; suffocation warnings if applicable.
4. Defect Classification
Critical: Safety issues (e.g., sharp objects).
Major: Broken stitches, incorrect sizing – likely to cause returns.
Minor: Minor thread pulls – may not affect usability.
5. Documentation
Inspection Report: Includes defect photos, measurements, and pass/fail status.
Corrective Actions: Supplier must address failures (e.g., rework/replacement).